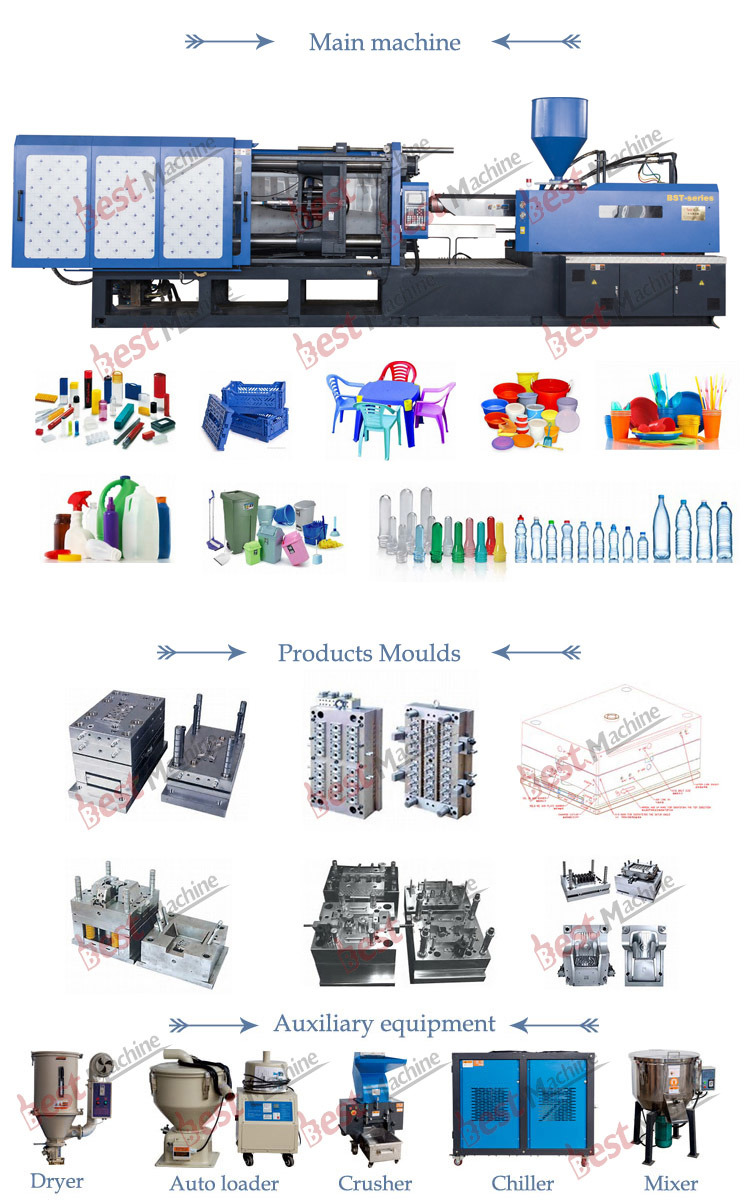
Feature/Specification
 Product performance and advantages:
-
Servo energy-saving system
Using the servo motor oil electricity composite structure
2. Servo motor high response feature
It costs only 0.05s for servo energy saving injection molding machines to achieve the maximum output, in comparison with conventional hydraulic injection molding machines. The response speed has been obviously increased, improving the production efficiency.
3. Unique function
Large colored screen with TFT interface
Full automatic close-loop control
Module design of hardware
Auto-tune PID temperature control
Pc interface USB, PIC, and FLASH…
Curve monitoring and analysis function
K-can data transmission (500Kbit/s)
On-line central monitoring function
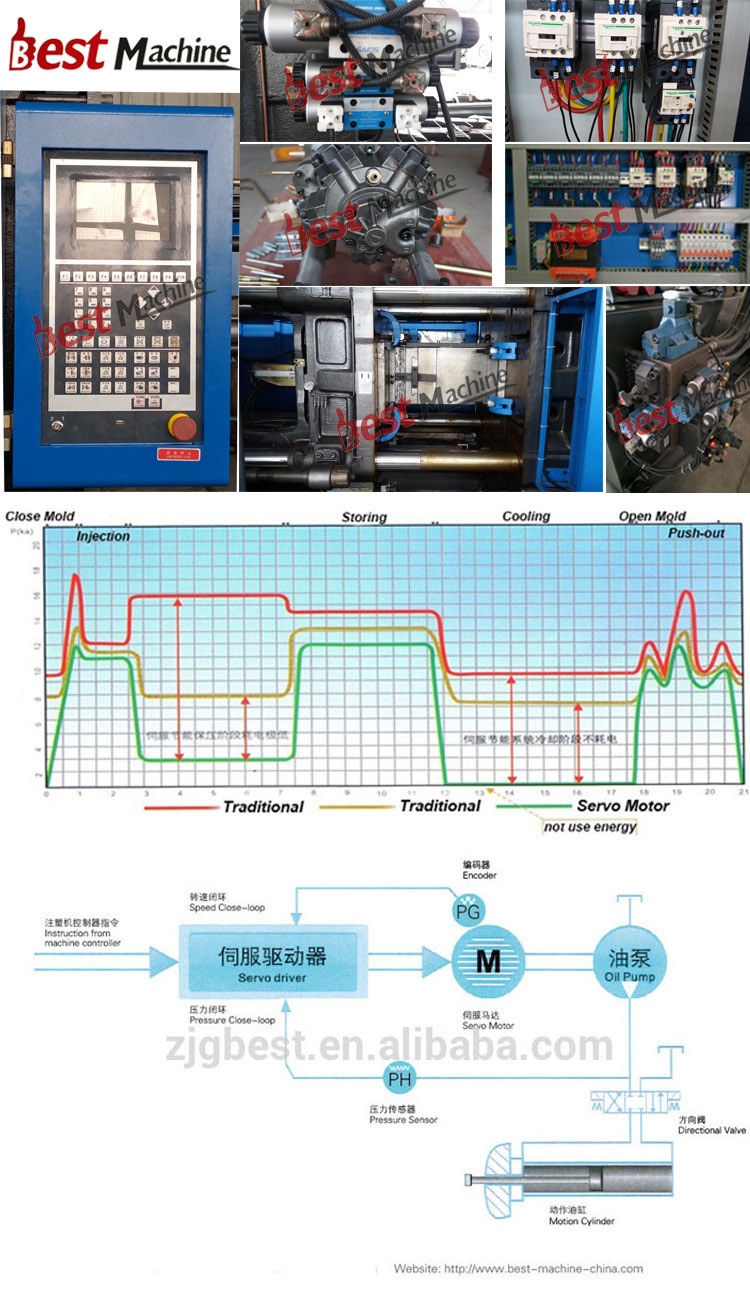
Technical Parameter
BST-3850A
INJECTIONÂ UNITÂ |
 |
A | B | ||||
Screw diameter | mm | 63 | 65 | ||||
Shot size(theoretical) | Cm³ | 1120 | 1190 | ||||
Shot weight | g | 1008 | 1072 | ||||
Injection pressure | Mpa | 175 | 165 | ||||
Injection rate | g/s | 320 | 340 | ||||
Screw L/D ratio | L/D | 22.7 | 22 | ||||
Screw speed | r.p.m | 0-160 | |||||
Nozzle Diameter | Srmm | 20 | |||||
CLAMPINGÂ |
 |
 |
|||||
Clamp tonnage | KN | 3850 | |||||
Toggle stroke | mm | 660 | |||||
Mould Thickness | mm | 280-680 | |||||
Space between tie-bars | mm | 680*680 | |||||
Ejector stroke | mm | 160 | |||||
Ejector tonnage | KN | 80 | |||||
Ejector number | Piece | 13 | |||||
Hole Diameter | mm | 160 | |||||
OTHERSÂ |
 |
 |
|||||
Heat power | KW | 17.5 | |||||
Max. pump pressure | MPa | 16 | |||||
Pump motor power | KW | 30 | |||||
Valve Size | mm | 25 | |||||
Machine dimension | m | 7.0*2.2*2.0 | |||||
Machine weight | t | 11.5 | |||||
Oil tank capacity | L | 400 |
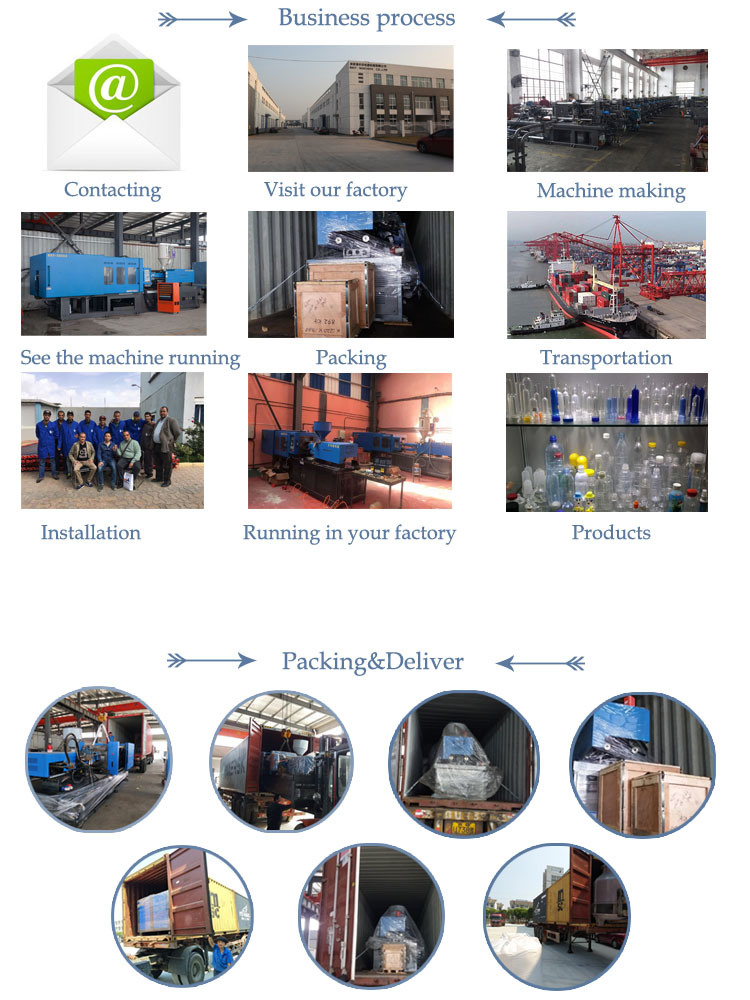
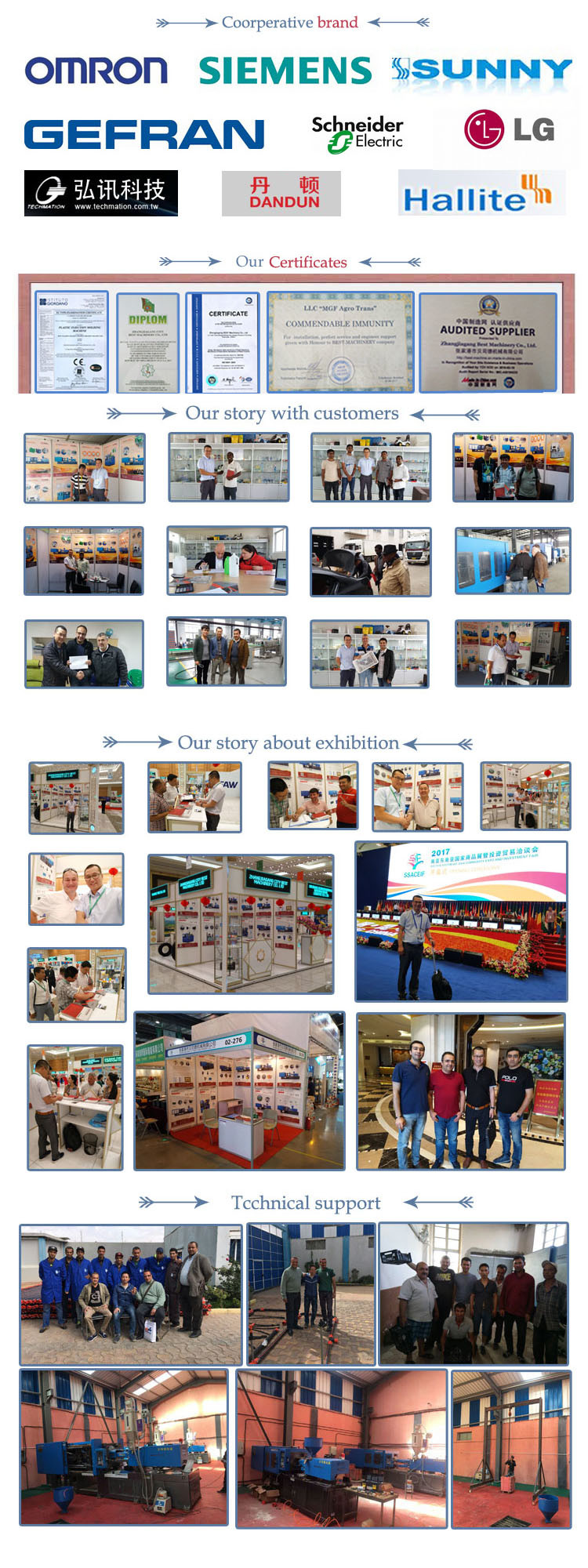
Terms&Condition
1. Payment Method
1. 30% by T/T as down payment within 7 days the contract signed
2. 70% by T/T paid before delivery
3. Or by order
2 . Mechanical Warranty
One year warranty and come with at least one year recommended spare parts
3. Delivery & Packing Â
Ø Delivery Time: 50-60 days after get down payment Ø Coming Document:
1) Machine Quality Guarantee
2) Complete set install & maintain instruction Book in English language
3) Complete Document for customer to clear its custom
Ø Packaging requirement:;
1) The special packaging box is according to the immunity standard in China,it suits for long-distance transport, damp proof, rustproof, land way and seawayÂ
2) Transportation ways: Sea transportation
4. Install in Spot
If Engineers install in spot
1) Installment USD100/day. Person as allowance
2) Training fee is free for customer's workers within the installation period
3) The tickets from China to the customer factory and return paid by the customer
4) The local housing , food, and transfer cost at customer factory paid by the customer
Â
A packed tower is a device used for the separation, purification, absorption, removal, or reaction of gases or liquids. It usually consists of a vertical cylindrical or square container and a packing layer. The filler layer can be of various shapes and materials, such as spherical, annular, grid shaped, plate shaped, etc., used to increase surface area and wettability to promote gas or liquid contact and mixing. Packed towers can be used for the following applications:
1. Absorption: Packed towers can be used to absorb pollutants in gases, such as sulfur dioxide, ammonia, hydrofluoric acid, etc.
2. Removal: The packed tower can be used to remove impurities in liquids, such as salts in water and impurities in oil.
3. Separation: Packed towers can be used to separate components from gases or liquids, such as oxygen and nitrogen in air, and different components from petroleum.
4. Reaction: Packed towers can be used for chemical reactions, such as acid-base neutralization, redox reactions, etc.
5. Distillation: Packed columns can be used to distill liquids, such as petroleum distillation, alcohol distillation, etc.
Separation Packed Tower,Anticorrosive Packed Tower,Industrial Packed Tower,High Efficiency Packed Tower
Yangzhou Tongyang Chemical Equipment Co., Ltd. , https://www.tongyangchemic.com