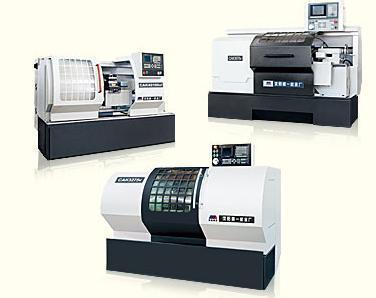
A high-end person in charge of a company official said that when assessing whether a country's machinery industry is strong, people tend to care about several aspects of performance. For example, whether it has mastered the core technology of independent intellectual property rights; whether it has strong technical capabilities in major equipment; whether it has a high share of high-end equipment, and whether the quality of its mainstream technology and equipment is in a leading position in the world.
It is true that according to this criterion, the machine tool industry is indeed not a small gap, especially the lack of confidence in the industry is the high-end machine tool market, it has been rare to have exciting news.
As the "mother of industry" - the indisputable of CNC machine tools, China can not completely autonomy in the manufacture of many high-end products. Highly efficient automotive engines, aircraft engine vortices, aircraft fuselages, nuclear power plant components, high-speed train heads, etc., all rely on foreign machine tools to varying degrees.
For example, the blades of a machining engine must be extremely accurate to ensure that it works properly under high temperature and high pressure. The blades also exhibit complex curved surfaces and must be machined by high-speed, ultra-precision, and powerful five-axis linkage machines. The same is true for nuclear power and gas turbine blades.
High-precision lenses required in the electronics industry and other fields, as well as processing of missile seekers, also require ultra-precise five-axis linkage machine tools; aircraft webs and wings require ultra-high-speed machine tools; large aircraft and nuclear power plant components require large pressure Machines; the manufacturing of composite materials needed for aerospace needs wire-laying machines... All the areas where China's manufacturing industry is relatively weak, and the lack of machine tool processing capability is the most critical obstacle.
In the face of this, the domestic high-end CNC machine tools are obviously "insufficient in gas." However, what needs to be stated is that this is not the lack of a single high-end machine tool, but the lack of a large number of high-end machine tool industrialization, market-oriented products are very competitive. Of course, this kind of argument needs to present an annotation. The Jinan No. 2 machine tool is no longer the same language.
On July 11th, Jinan No. 2 Machine Tool announced that following the inclusion of two Ford cars in Kansas and Detroit in the United States in 2011, all five large-scale stamping line orders had been awarded to the Ford Motor Company's large-scale stamping line project at the Kentucky factory in the United States.
It is reported that the factory has been using two stamping production lines made in Germany. This time, Ford Motor Company chose to make in China.
People in the machine tool industry understand the significance of the automotive market for metal-cutting machine tools. According to many years of historical experience, nearly half of the general domestic metal cutting machine tools are supplied to the automotive industry. However, sadly, the domestic machine tool industry rarely enters key areas such as engine production lines. At China's OEMs, most of the equipment required for the four major processes (press, welding, painting, and final assembly) needs to be imported.
By analyzing the successful experience of Jinan No. 2 Machine Tool, it is not difficult to find that the reason why it can win glory for domestic machine tools in the international market is not unrelated to its successful support in the domestic automobile market. After all, Jinan No. 2 Machine Tool Co., Ltd. has occupied more than 80% of the market share in the field of domestic automotive CNC punching equipment.
We are also very clear that many leading companies in the automotive industry in China have a background in joint ventures, which lays the foundation for the Jinan No. 2 machine tool to go out and allow foreign car giants to purchase their products with confidence.
In recent years, the state has given a lot of encouragement policies to the machine tool industry, which helps the domestic machine tool companies to make efforts in the high-end market. For example, according to the “High-end CNC Machine Tools and Basic Manufacturing Equipment†special plan, by 2020, about 80% of the high-end CNC machine tools and basic manufacturing equipment required for aerospace, shipbuilding, automobile, and power generation equipment manufacturing will be based in China.
Who is the main bearer of these responsibilities? The answer is undoubtedly the vanguard of all sub-sectors. And these are mostly beneficiaries of major special policies.
Of course, through the display of major transformation achievements in recent years, we have indeed seen the emergence of a large number of outstanding achievements, and their single technical indicators are also worth noting. The only thing that is regrettable is the lack of marketization and industrialization. In other words, it is not enough.
There are many reasons for the overwhelming existence of this status. Among them, many reflect the fact that small and medium-sized customers cannot afford it, while large enterprises do not dare to use it.
The former is well understood, because high-end CNC machine tools are expensive, although prices have advantages over similar imported products, but simply on the high prices, it is not a small expenditure. “There is no way that our key parts and components for this machine are imported from abroad and the cost itself is very high.†Someone in a company is helpless.
“But even the simplest parts, once used on precision machine tools, must reach a certain degree of precision. The functional components required for CNC machine tools, such as bearings, pendulum heads, and gratings, are difficult to create in China. The products. So for these customers will often limit the brand configuration."
The most common components such as screws, guide rails, and cutting tools have not improved. This is a cost-effective solution for Chinese companies that are committed to building high-end CNC machine tools.
Therefore, we cannot complain that domestic machine tool manufacturers do not work hard. Actually, since last year, the growth of domestic machinery industry has been slowing down. Many tactile and sensitive machine tool companies have already felt that with the transformation and upgrading of China's national economy, the initial needs of industrialization The explosive growth period is about to pass. The requirements for equipment and quality in various industries will become higher and higher. The Chinese high-end CNC machine tool market will become a battleground for military strategists.
In this atmosphere, transformation and upgrading have become a consensus. The next step is how each one will turn, which direction to turn, and how the user will be able to handle any practical problems.
It is the most unreasonable behavior to blame users for not adopting. After all, the user is God, and there are users wrong. The only remaining problem is how to fight for opportunities.
The key projects may be the primary recommendation sites for high-end products of various companies because of their obvious demonstration benefits. However, it is also an indisputable fact that competition is high and the threshold is high.
For this reason, some companies proposed the idea of ​​putting machine tools into the factory for free trials in the early stages of the tendering company, in order to gain the trust of customers.
But this is just a point-to-point trick. It is best to give feedback to the industry. The best solution is to provide the entire production line. However, this is obviously not on a single level in terms of the difficulty of single-machine supply. The latter requires the improvement of all-round capabilities of the company. Therefore, this is also the reason why the key enterprises in the industry need to assume the first position in the high-end domestic machine tool industry.
However, for domestic machine tool companies, a good news is that in recent years, the state has formulated a series of policies in areas such as bidding and procurement of major construction projects to encourage the improvement of localization. It is stipulated that the localization rate of related products must reach a certain target in order to participate in bids for major construction projects and enjoy preferential tax rebates for imported components.
However, as we often say, there are policies and downstream measures.
In the face of a demanding Chinese market, some overseas multinational companies have taken countermeasures and made breakthroughs in breaking through China’s “localization rate†review and occupying the high-end market in China.
In other industries, for example, in the field of wind power equipment, the state requires that the “localization rate†of wind turbine manufacturing be over 70% before it can participate in wind power project bidding. However, some foreign-funded enterprises entering the wind power market in China set up factories and set up joint ventures locally. Or to provide suppliers with licensing and drawings of the OEM method, they will be able to successfully pass the “localization rate†review and get the wind power construction project. The localization rate has become the local supply rate of wind turbine components rather than the real state-owned intellectual property ratio. The key core technology has not been grasped by local Chinese companies.
In the field of nuclear power, the state vigorously promotes the independence of nuclear power technology and equipment, and has a clear requirement for the “localization rate†of equipment. It objectively encourages project owners to prioritize the purchase of domestically produced goods when purchasing nuclear power equipment. However, overseas nuclear equipment enterprises can meet the "domesticization" requirements for nuclear power equipment procurement in China through joint ventures and cooperation with local companies. However, in fact, such cooperation often does not really involve the transfer of core technologies. The core technology is still in the hands of foreign parties.
It can be said that in such Sino-foreign cooperation, the focus of both parties can be described as tacit. This is to allow the joint venture products to be labeled with localization and participate in bidding for construction projects. While peeling off its localized labels, the core is still an authentic imported product, and after these bends, it will be "localized."
Under this multi-faceted struggle, many companies developed prototypes that became a must-have song. Although in previous reports, products such as filling domestic gaps and reaching internationally advanced levels have appeared in an endless stream, reports on the marketization of products have rarely been reported.
In fact, in the Chinese machine tool manufacturing industry is not so lack of high-end technology, nor is it so lacking in high-end products today, if the reason that imported machine tools are still monopolizing China's high-end market is attributed to design capabilities and technical levels, it is clearly unfair.
Compared with the vigorous R&D and redesign, it is the ubiquitous light manufacturing and light technology phenomenon in China's machine tool manufacturing industry. This and the past a period of time, the enterprise is difficult to contain the scale of impulse, so that companies have become very impetuous and closely related.
For example, some companies took the lead in the word, no matter whether the process is perfect, whether the process is reasonable, whether the processing equipment is in place, and whether the technicians are adaptable. Once the new product passes the appraisal, it will be eager to industrialize and grab the market on scale, lest it lose opportunities. The result is often contrary to expectations, causing a hum.
In this way, serious illnesses and illicit illnesses will inevitably continue. As a direct result, the reliability of the machine tool products must become unreliable. When the user only buys the domestic high-end CNC machine tools, it is only a cheap map. Looking forward to high-end but not high-quality domestic CNC machine tools to completely replace imports, has become a luxury.
As long as the manufacturing process is still short, high-end technology will shrink, and high-end design will also be discounted. Therefore, to truly make the domestic high-end machine tools truly market-oriented, we must make a real change from the mentality.
Vertical injection molding machine is a mechanical device. Usually composed of injection system, mold clamping system, hydraulic transmission system, electrical control system, lubrication system, heating and cooling system, safety monitoring system, etc.
Special Injection Machine, Filter Injection Molding Machine,Molding Machine Oil Filter,Plastic Injection Machine
Changzhou Yuehai Zanyang Machinery Sales Co., Ltd. , https://www.zanyangmachine.com